Ear Plugs: Custom or Manufactured: That is the Question?
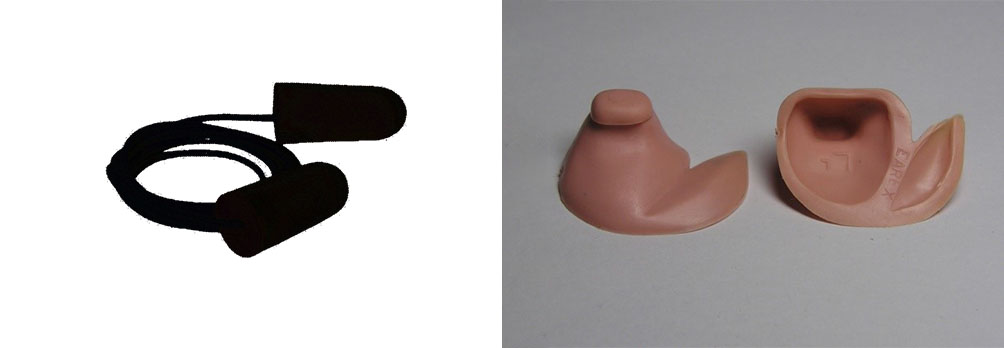
So, you have decided that you need hearing protectors. After carefully considering and agonizing over the choice of plugs or muffs, you have opted for the plugs: they are lighter and not as hot as the muffs, something highly desirable, especially in summer!
Now is the time to choose amongst the two large groups:
- factory-made (or manufactured) and custom made, and
- custom made.
The factory-made protectors are mass-produced, meaning that the user fits them and has to choose the size that is right for him. The others, the custom-made devices, are individually sized and adjusted to the user’s ear canal.
The factory-made plug can be divided into the following groups:
a) Foam — these devices, also called “rolldown” plugs, are made from foam material that recovers slowly to it's original size once deformed. Such products need to be rolled and tightly compressed before insertion in the ear canal. Once inserted, they expand and fill the cavity. Although often referred to as “disposable plugs,” they can be reused a few times. They are sold both as one-size-fits-most and in a range of sizes to fit most ears. In either case, they should be individually sized for the person’s ear. Examples of foam earplugs are shown in Figure 1. (Source: Figure 1, CSA Z1007:16 (R2020), Hearing loss prevention program (HLPP) management. © 2016 Canadian Standards Association. Please visit store.csagroup.org)
b) Push-to-fit — These devices are composed of similar foams to those used in rolldown earplugs. They consist of a pod, dome, or conical shroud with a flexible stem that facilitates the insertion of the plug into the ear canal. Examples of push-to-fit earplugs are shown in Figure 2. (Source: Figure 2, CSA Z1007:16 (R2020), Hearing loss prevention program (HLPP) management. © 2016 Canadian Standards Association. Please visit store.csagroup.org)
c) Premoulded — These earplugs, also known as reusable earplugs, are formed from flexible materials into conical, bulbous, or other shapes, often with one or more flanges or sealing rings, which are typically affixed to or enshroud on a flexible stem for handling and insertion (see Figure 3). They are sold both as one-size-fits-most and in a range of sizes to fit most ears. Whether available in various sizes or one size, they should be individually sized for the worker’s ear. (Source: Figure 3, CSA Z1007:16 (R2020), Hearing loss prevention program (HLPP) management. © 2016 Canadian Standards Association. Please visit store.csagroup.org)
The fact that there are different groups and so many types in each indicates that there is no clear advantage for using any of them: they are all good, provided they are worn and worn correctly.
As mentioned in a previous article, the two most important properties of a hearing protector are attenuation and comfort. However, while attenuation is a measurable characteristic, comfort is not. That is another reason for the wide variety of plugs available: peoples’ preferences are based in many instances on personal reasons that are not always objective. That is why one protector is preferred as opposed to another. This is so, up to the point that hearing conservation programs in workplaces recommend that more than one type of protector be made available for the employees to choose from (all acceptable from the attenuation point of view)!
And now, after discussing the factory-made devices, let’s examine the custom-made family of plugs.
Custom-molded earplugs are intended to fit precisely a particular ear. Most are made using silicone, vinyl, or acrylic compounds. Another class, called “molded in place” uses a putty-like material that hardens to become the final product. Ear canal impressions are made using a viscous material injected into the ear canal and cures in about 5 min.
As with any plug, attenuation is of utmost importance. And here resides one of the problems with this kind of device: the shape of the plug depends on the skill of the person who makes the mold. Since this shape neither changes nor adapts to the ear canal's physical size, if the mold is not manufactured correctly, the attenuation will suffer, and so will be the hearing of the person to be protected.
Here is another potential problem with the custom-molded devices. The shape of the ear canal is not invariable forever: it changes with time. Also, there is a mechanism of self-defense regarding the foreign object – the plug – inserted in the canal: reduce the point of contact between the plug and the earcanal. The net result is again a reduction of the attenuation.
It has to be noted that there are also significant advantages to the custom-molded plugs. First, they are molded individually for the left and the right ear, meaning that any difference in the size or shape of the earcanal is taken care of. (This can also be considered a disadvantage since plugs are not interchangeable, and the wearer has to be careful to fit them on the appropriate ear). Finally, from the purely psychological point of view, users tend to be proud of having something done individually for them. Also, there are indications that they tend to use them more often than those with factory-made devices.
In conclusion: this author has no particular preference for any of the above-described earplugs. They are all acceptable, and they all provide adequate attenuation to the wearer if properly worn. And here, we have to once more remember the sage saying of Aram Glorig: the best protector is the one that is worn and adding: “… and properly worn”.
Note: Figures are used with the permission of Canadian Standards Association, (operating as “CSA Group”), 178 Rexdale Blvd., Toronto, ON, M9W 1R3, material is reproduced from CSA Group standard CSA Z1007:16 (R2020), Hearing loss prevention program (HLPP) management. This material is not the complete and official position of CSA Group on the referenced subject, which is represented solely by the Standard in its entirety. While use of the material has been authorized, CSA Group is not responsible for the manner in which the data is presented, nor for any representations and interpretations. No further reproduction is permitted. For more information or to purchase standard(s) from CSA Group, please visit store.csagroup.org or call 1-800-463-6727