Occupational Audiology in the United States
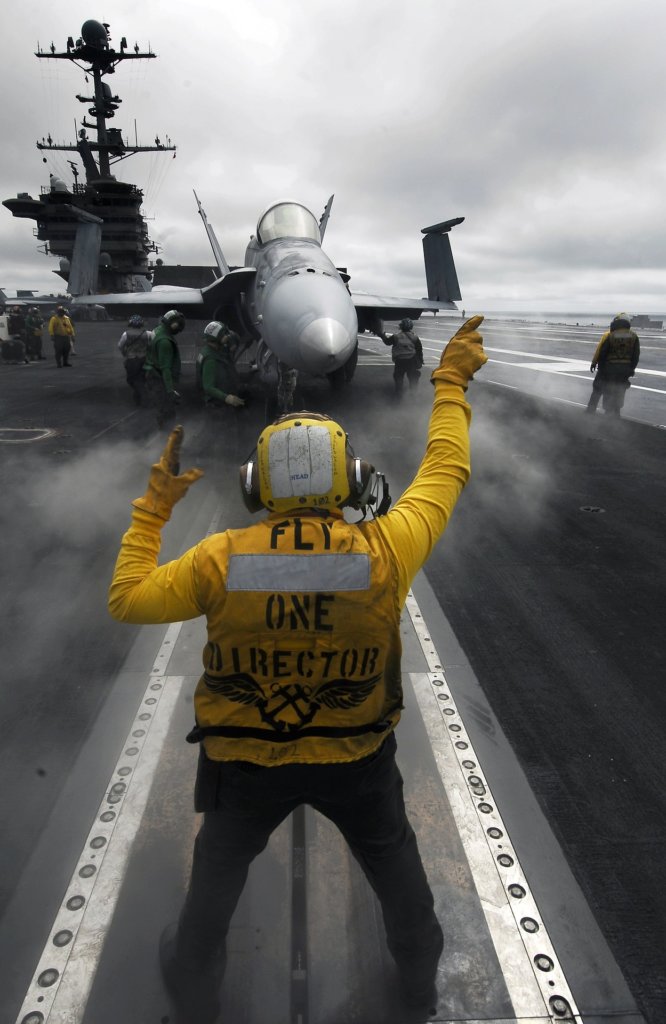
When I was asked to write a piece about being an occupational audiologist in the United States, it took me quite some time to decide exactly what to say (which, as my colleagues would likely confirm, is unusual for me because I pretty much always have something to say about everything). I have practiced as an audiologist for 18 years, and I have spent a good majority of those years working full-time on the hearing conservation side of the profession, first for several privately owned businesses and currently as a civilian employee of the US Department of Defense (DOD). As with any other area of audiology, there are challenges, but the variety of the work, the people with whom I get to do this work (both colleagues and patients), and the primary mission of preventing hearing loss before it impacts an individual’s quality of life, makes it pretty easy to overcome whatever challenges are thrown my way.
Learning the Ropes
I think the best place to start when talking about occupational audiology in the US is with the training offered for those interested in this area of audiology. I clearly remember that when I decided to become an audiologist, I knew that hearing conservation was where I wanted to focus. Yet, to my surprise, of all the graduate school courses I was expected to take, only one class was dedicated to noise exposure and hearing conservation. A recent informal poll of audiology colleagues confirmed my suspicion many audiologists in the US take only one graduate-level course on these topics.
This begs the question – how do we prepare our audiology students to successfully work in hearing conservation with the limited course offerings available to them? Better yet, how do we let our students know that occupational audiology can be a full-time job when the focus of graduate studies is heavily concentrated in other areas of our profession? For me, the answer was simple – to the greatest extent possible, I made every single graduate school paper, project, independent study, and my final year Capstone project focus in some way on noise and hearing conservation. I sought out an industrial hearing conservation company for one of my clinical placements during graduate school to ensure I had some hands-on experience before graduating. In these ways, I could carve my own path through graduate school to ensure that I was prepared to work in the area of audiology that interested me the most.
The path may not be as straightforward for other students, who may not have come into the field with an interest in occupational audiology. Because of this, I have taken as many opportunities as possible to supervise audiology students and externs. My goal is to provide them with experience working on the hearing conservation side of audiology and encourage them to personalize their studies whenever possible to get the most from their graduate school experience.
A Day in the Life
An understandable side effect of the minimal graduate school training about hearing conservation in the US seems to be limited knowledge of exactly what an occupational audiologist does. In case you’re wondering – occupational audiology involves much more than performing puretone air conduction audiograms on noise-exposed workers! Throughout my career, I have had the opportunity to do everything from conducting noise monitoring, fitting hearing protection – both custom and non-custom fit products, educating both employers and their employees on the importance of hearing conservation, and evaluating changes in hearing thresholds for potential work-relatedness and recordkeeping requirements. The job has also involved writing interpretations of various hearing conservation regulations, preparing opinions on workers compensation claims for hearing loss, training and supervising audiometric technicians, and – of course – performing occasional puretone air conduction audiograms on noise-exposed workers. Because there is such a wide variety of job responsibilities, I can say without hesitation that working as an occupational audiologist is rarely boring.
Of all these potential job duties, I have always found conducting noise monitoring to be the most enjoyable. In the US, noise monitoring is typically conducted by occupational audiologists or industrial hygienists and involves going onsite to a client’s location and touring the entire facility to take noise measurements. Those measurements include the Time-Weighted Average (TWA) noise exposure levels of workers and the instantaneous sound levels of individual pieces of equipment. The data obtained from noise monitoring is used to develop other aspects of an employer’s Hearing Conservation Program (HCP). The fun part comes from being onsite, which allows the audiologist to speak with noise-exposed workers to learn more about their experiences and needs regarding hearing conservation. It also provides a fascinating look into production and manufacturing in various industries – have you ever wondered how plastic straws are made? Or how much butter is in a croissant? (Hint: it’s a LOT of butter!)
In my current role as a civilian DOD employee, I work as the Occupational Audiology Department Head for Norfolk Naval Shipyard (NNSY) in the Hampton Roads region of Virginia. Our three-person department is located within the NNSY Branch Health Clinic and consists of two Hearing Conservation Technicians and me. The technicians’ primary role is to provide routine air conduction audiograms, hearing conservation education, and hearing protection device fitting to civilian NNSY employees and service members stationed at NNSY or other commands in the area.
As the Occupational Audiologist, I split my time between patient care and program administration. In terms of patient care, I review abnormal audiograms brought to me by the technicians and perform comprehensive audiometric evaluations on individuals with changes in hearing, possible medical pathologies, or other needs for further testing. On the program administration side, I work closely with the NNSY Safety Department to ensure program requirements are met and discuss opportunities for improvement. This includes site visits to various shops throughout the NNSY, allowing me to speak to noise-exposed employees and supervisors to increase the HCP’s visibility.
I also routinely collaborate with the other DOD occupational audiologists in this region to participate in outreach events, earmold shoots (during which we may take 50-60 sets of impressions in one morning) and teach the DOD-required hearing conservation technician certification course. Working with the amazing team of occupational audiologists here in the Hampton Roads region has been a rewarding experience so far – almost as enjoyable as watching layers of butter get folded into croissant dough!
The Uphill Battle
Much of what occupational audiologists in the US do is guided by federal regulations. With a few notable exceptions (including the DOD), the Occupational Safety and Health Administration (OSHA) “Hearing Conservation Amendment” (29 CFR 1910.95) applies to the majority of noise-exposed workers in general industry throughout the US. Having a federal agency define the requirements for HCP provides some degree of consistency and simplifies compliance across the country. At the same time, individual states and territories are permitted to create their own regulations, provided that they are at least as effective as the OSHA regulation (https://www.osha.gov/stateplans). OSHA outlines the five major components that are required for HCP. These requirements include Noise Monitoring, Audiometric Testing, Hearing Protection, Training, and Recordkeeping. Occupational audiologists can be involved in any or all of these required HCP components, depending on their specific job setting, allowing us the great range of potential responsibilities mentioned earlier.
One interesting aspect of the OSHA regulation is that although it details the requirements for an employer’s HCP to be compliant with the law (therefore avoiding violations and fines), those requirements are not necessarily in line with best practice for hearing conservation, as defined by the National Institute of Occupational Safety and Health (NIOSH), which functions as the research arm of OSHA (Table 1). The discrepancy between OSHA requirements and NIOSH recommended best practice can create some challenges when working with clients whose priorities may differ from the occupational audiologist’s priorities.
In my personal experience, I have seen many private companies in the US that do not have resources allocated to hire safety professionals to manage their various occupational safety and health programs. In these companies, the duties that would typically fall to a safety professional are delegated instead to other personnel, such as Human Resources (HR) employees, who may or may not have received any formal training in safety. Given this, it is not surprising that their knowledge may be limited to the requirements for OSHA compliance rather than the recommendations for best practice. This creates both a challenge and an opportunity to educate these professionals on the importance of hearing conservation. Over time, with consistent messaging, I have seen many of these professionals gain an appreciation for the work of occupational audiologists and can effectively pass down that appreciation to noise-exposed workers at their companies.
As alluded to above, DOD personnel are covered by different regulations (known as instructions) than those issued by OSHA. DOD Instruction 6055.12 “Hearing Conservation Program” outlines the general requirements. In broad strokes, the DOD Instruction follows the NIOSH recommendations for best practice much more closely than the OSHA regulation (Table 1). Using the DOD Instruction requirements as the foundation, each branch of military service has developed its own HCP Instruction to meet the specific needs of their personnel.
Working with a military population brings unique challenges to managing an HCP. In addition to individual quality of life, hearing loss prevention in the DOD is essential in maintaining overall mission readiness for both military service members and civilian personnel. Unfortunately, hearing conservation can sometimes become an afterthought with the myriad of other physical requirements for mission readiness. This is where outreach events, site visits, annual HCP training, and other educational opportunities play a key role in the success of the HCP. By working daily to increase awareness of the importance of hearing ability to mission readiness, we aim to keep hearing conservation closer to the top of mind for service members and civilian employees.
The Key to It All
In the world of occupational audiology, we often preach that the most important part of every HCP is education. I truly believe this is the case, and it goes much deeper than simply training noise-exposed workers how to wear earplugs. In my years as an audiologist, I have been fortunate enough to play a small role in educating those noise-exposed individuals, the program managers, and other professionals that implement OSHA, DOD, and other regulations that guide their HCP. In addition, I have had the opportunity to participate in the education of audiology graduate students and externs, hopefully contributing to their knowledge of occupational audiology and perhaps even sparking an interest for some of them in pursuing this area of audiology. Last, but not least, I hope that I have been able to share my experiences and maybe a tiny bit of education about occupational audiology in the US with you, my Canadian colleagues. Now, I think I need a croissant.
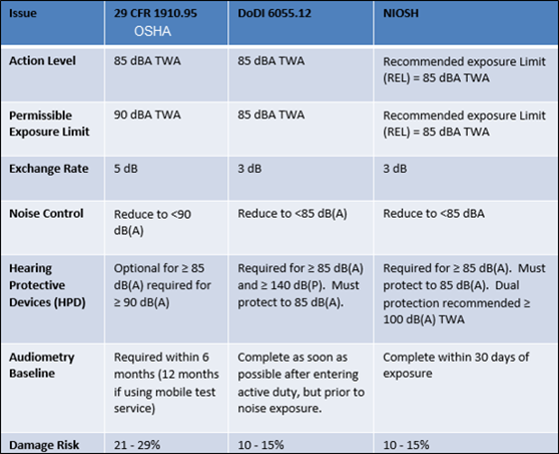
Disclaimer
The views expressed in this article are those of the author and do not necessarily reflect the official policy or position of the Department of the Navy, Department of Defense, or the United States Government.
I am an employee of the US Government. This work was prepared as part of my official duties. Title 17 USC 105 provides that “Copyright protection under this title is not available for any work of the United States Government.” Title 17 USC 101 defines a United States Government work as a work prepared by a military service member or employee of the United States Government as part of that person’s official duties.
References
DODI 6055.12. Hearing Conservation Program (HCP). DODI 6055.12 (2019).
Murphy WJ and Franks J. NIOSH Criteria for a Recommended Standard: Occupational Noise Exposure, Revised Criteria The Journal of the Acoustical Society of America 2002;111(5):2397-2397. DOI:10.1121/1.4778162
Occupational Safety and Health Administration. Occupational Noise Exposure, 29 CFR 1910.95 (1983).
Occupational Safety and Health Administration. (n.d.). State Plans. Available at: https://www.osha.gov/stateplans