Uncovering the Complexity of Micro-Electronic-Mechanical Systems (MEMS) Microphones
Reprinted with kind permission from INNOVATIONS | VOLUME 5 | ISSUE 1 | 2015
Modern technology has redefined our clinical expectations of hearing aids. The microelectronics that have made these advancements possible are staggeringly complex. A multitude of connections wind through each integrated circuit, combining passive components with active components to adequately regulate voltage and communicate with an array of transducers: microphones, magnetic field detectors, receivers, wireless radios and antennas. The designers of yesterday’s hearing hardware would scarcely recognize the technology of today. Though seldom mentioned in this evolution, microphone technologies have also seen advancements. The modern electret microphone, for instance, has become smaller with little decrease in sensitivity or dynamic range; and recently, the telecommunications industry has begun a shift away from the traditional electret microphone toward a microphone technology based on a micro-electronic-mechanical system (MEMS). MEMS technology describes a group of microminiaturized electromechanical systems that enable sensors or processors to be fabricated using methods traditionally used to produce semiconductor devices such as microprocessors. The application for this technology ranges from light sensors to accelerometers to the microphones used in today’s most advanced mobile phones, to the microphones used now in hearing aids.
The manufacturing processes used for MEMS microphones allow higher quality control than those used with electret microphones. These techniques include chemical etching and lithography. In the case of wet chemical etching, wafers of silicon, which are microns thick, are dissolved in a highly controlled manner by powerful acids or bases. The process is so accurate that microscopic structures are created in the silicon itself. Lithography uses photosensitive materials that change properties when exposed to light. Often the lithographic process will be used to define microstructures on the MEMS product prior to wet etching. Processes such as these allow for thousand of microphones to be produced as a single batch. In contrast, electret microphone production requires the manual assembly of individual microphones using adhesives and plastics. These adhesives and plastics are the components of an electret microphone that are most impacted by environmental conditions.
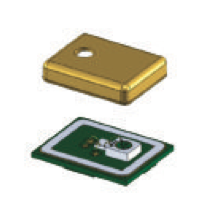
Figure 1. Exploded view of a MEMS microphone.
The properties of the silicon used in creating MEMS components are a large part of what makes the technology compelling. For instance, the material properties of silicon are similar to those of steel in many regards; the two materials share similar yield strength and thermal conductivity, whereas silicon features greater resistance to hysteresis and warping (Bryzek, 2005). Figure 1 is an illustration of a single MEMS microphone. The effects of these traits on the comparative performance of electret and MEMS microphones are discussed below.
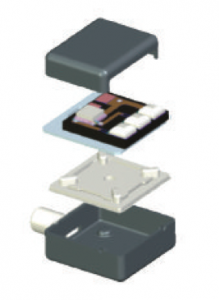
Figure 2. Exploded view of an electret microphone
The electret microphone, which is shown in Figure 2, consists of a polyester (i.e. Mylar) diaphragm that has been stretched and adhered to a retention ring. This diaphragm is similar in concept to the eardrum — sound pressure that impacts the diaphragm causes it to vibrate. The distance between this diaphragm and an electrically charged backplate changes with that vibration; this change in distance between the backplate and diaphragm results in a change in voltage that is analogous to the change in sound pressure. In order to accurately reproduce acoustic energy, the electret microphone’s diaphragm must maintain a specific tension and the backplate a specific voltage. However, changes in humidity and temperature affect the tension of the polyester diaphragm. This results in changes to the microphone’s sensitivity and phase response. While it is unlikely that these changes would have an audible impact on a hearing aid’s frequency response, they will impact other aspects of hearing aid performance.
Directional processing in hearing aids is achieved by leveraging phase relationships between two microphones that are separated by a few millimeters and aligned along the horizontal plane. Differences in the arrival time of sound to each of these microphones allow for directional microphone processing that suppresses sounds arriving from behind the listener. When the microphones used in this process are not identically matched in sensitivity and phase, the effectiveness of directional processing is greatly reduced.
Electret microphones are manufactured to specifications that, upon leaving the factory, are well suited for use in a directional microphone array. However, the polyester diaphragm of the electret microphone tends to absorb moisture in hot, humid conditions. Thus, changes in environmental humidity result in changes in microphone sensitivity. This change contributes to the mismatch between microphones and degrades the performance of the directional systems. MEMS microphones do not use the tension-dependent single diaphragm. Instead, these microphones use crystalline discs to transduce sound (Figure 3). Each disc is less than one millimeter in diameter, approximately the size of a grain of sand. The disc array functions as a single system, capturing acoustic energy and translating it into an electrical signal that can be used by the hearing aid. The physical properties of silicon make the system resistant to the effects of temperature and humidity.
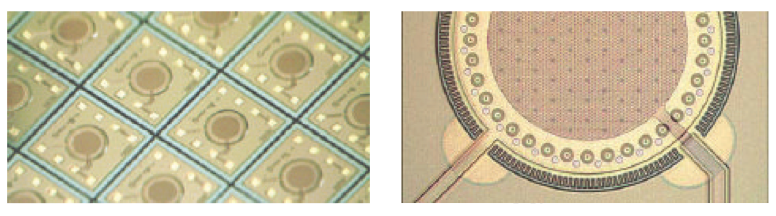
Figure 3. A sheet of crystalline diaphragms that will become MEMS microphones, shown at high magnification.
An additional difference between these microphone styles relates to the backplate mentioned earlier in this discussion. The backplate is an electrically charged surface that sits behind any microphone’s diaphragm. The distance between the microphone’s diaphragm and the charged backplate affects the sensitivity of the system to incoming sounds. In the case of electret microphones, the backplate is coated in an electret material that has a semipermanent electrical charge. In order to maintain sufficient sensitivity to the incoming sound, the electret material must maintain an electrical potential upward of 350 volts. This high voltage is necessary because of the relatively large distance between the backplate and diaphragm. The manufacturing accuracy and rigidity of the MEMS diaphragms allow the separation distance between the diaphragm and backplate to be greatly reduced, allowing the microphone to operate with a highly efficient 10-volt charge that is maintained by a single charge pump instead of the high-capacitance electret material.
Additional benefits of MEMS microphones include the opportunity to connect the microphone directly to the flexible material that houses the hearing aid’s microprocessors with a reflow process, removing the need for soldered wires. The reflow process is one commonly used in the manufacturing of circuit boards. Instead of requiring manual soldering and attachment of microphone parts to the board, a system is constructed using a solder paste that temporarily holds components in place. When exposed to a controlled heat, the dry solder becomes liquid and affixes each component to the board. The process is extremely fast and more accurate than manual production. This process is not possible with electret systems that use plastic components and adhesives.
The implementation of MEMS microphones in hearing aids is the result of broad technology scanning, adoption and application to hearing care — a deliberate merger of technologies that were first developed for use in semiconductors and telecommunications. Hearing aids are a unique application that presents demands too strict for most technologies that originate in other fields. This is one example where a technology, most often used in telecommunications, could be reimagined and greatly optimized for use in the treatment of hearing loss. The result is a fundamental improvement in hearing aid design with a system that has better performance and is more stable over a wide range of environmental conditions than the electret microphones used until now.
Acknowledgements
The authors would like to thank Tom Burns, Wei-Li Lin and Aaron Schroeder for their contributions to early versions of this paper.
Reference
Bryzek, J. (2005). Principles of MEMS. In Sydenham, P. & Thorn, R. (Eds.), Handbook of Measuring System Design. Hoboken, NJ: John Wiley & Sons.